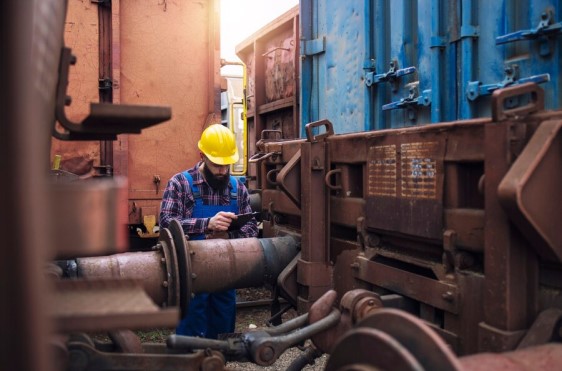
Maintaining industrial fluid transport systems is essential for smooth operations and extended equipment life. These systems often include industrial machine hoses and sewer pump supply, both critical components that require regular attention. Let’s dive into best practices to keep everything running efficiently.
Regular Inspections and Monitoring
Consistent inspections are the foundation of effective maintenance. Examine industrial machine hoses for signs of wear, cracks, or leaks. Small issues, if left unchecked, can escalate into major problems. For instance, a tiny crack in a hose could lead to significant fluid loss and operational downtime. Use visual inspections combined with pressure tests to ensure hoses are in optimal condition.
Proper Installation Techniques
Installation plays a crucial role in the longevity of industrial fluid transport systems. Ensure that industrial machine hoses are installed correctly according to the manufacturer’s specifications. Improper installation can cause stress on the hoses, leading to premature failure. For example, a hose that is kinked or twisted during installation might not perform as expected and could fail under pressure.
Routine Cleaning and Maintenance
Dirt and debris can accumulate in fluid transport systems, leading to clogs and inefficiencies. Regularly clean industrial machine hoses and associated components to prevent buildup. This is particularly important for Sewer Pump Supply systems where debris can easily cause blockages. Use appropriate cleaning agents and methods recommended for the materials of your hoses and pumps.
Fluid Quality and Compatibility
The type of fluid transported through your system impacts its performance and lifespan. Ensure that the fluids used are compatible with the materials of your hoses and pumps. For instance, using corrosive fluids with hoses not designed for such conditions can result in rapid deterioration. Always check the fluid specifications and ensure they align with the manufacturer’s recommendations.
Timely Replacement of Worn Parts
Even with the best care, some components will eventually wear out. Regularly replace worn or damaged industrial machine hoses and parts of your sewer pump supply system. This proactive approach helps avoid unexpected breakdowns. For example, if a hose shows significant wear or damage, replace it before it fails completely, potentially causing system downtime.
Training and Best Practices for Operators
Proper training for operators is crucial in maintaining fluid transport systems. Ensure that everyone handling the equipment understands best practices for operating and maintaining the system. This includes knowing how to properly handle hoses, recognize signs of wear, and follow maintenance procedures. A well-informed operator is less likely to inadvertently cause damage to the system.
Monitoring System Performance
Keep an eye on the overall performance of your fluid transport system. Use monitoring tools and gauges to track pressure levels and flow rates. Any deviations from normal operating conditions can be an early indicator of a problem. For example, a sudden drop in pressure might suggest a blockage or a leak in the system. Early detection allows for timely intervention.
Addressing Leaks Promptly
Leaks in industrial fluid transport systems can lead to significant issues, including fluid loss and environmental hazards. Address leaks as soon as they are detected. Depending on the severity, this may involve repairing or replacing hoses or components of the sewer pump supply system. For instance, a leaking sewer pump can lead to backups and potential contamination, making prompt repairs essential.
By following these best practices, you ensure that your industrial fluid transport systems operate smoothly and efficiently. Regular inspections, proper maintenance, and timely repairs are key to avoiding disruptions and extending the life of critical components like industrial machine hoses and sewer pump supplies.